Keith W. Dodson
Vice President of Business Development at AST (Automated Systems of Tacoma)
With over 26 years of total pharmaceutical experience across multiple dosage forms, Keith joined AST in May 2020 to lead the global business development team for AST's aseptic multi-formal filling systems. Prior to joining AST, Keith served in both technical and business development roles with companies including Thermo Fisher, Catalent, and 3M Company. Keith holds a Bachelor of Science in Mechanical Engineering as well as MBA from the University of Chicago.
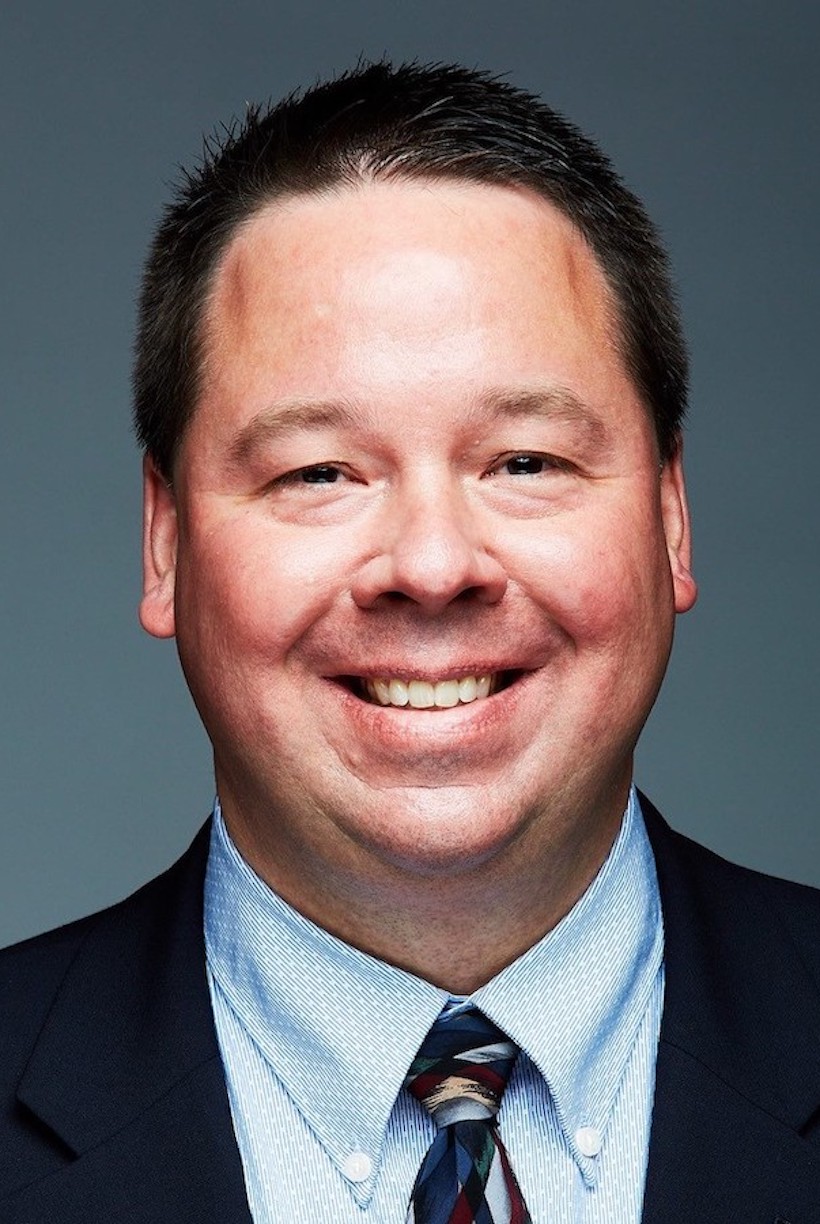
Title: Use of Robotics in Flexible Format Aseptic Filling
Robotic Automation in Aseptic Filling:
- Robotic arms are VHP compatible and can be sterilized in place
- Finely tuned programming of critical motions along all axes using teach points and recipes
- Speed and repeatability – extremely precise in following the same motions every time, within ±0.05 mm
- Functional safety – integrated pre-programmed safety features monitors advanced safety conditions based on position and speed of arm
- Hands-off processing, operators simply need to set up the machine and let the robots handle the entire fill-close process
- Greatly reduced footprint – Robots allow for optimal utilization of space by allowing you to use one system for multiple processes and are not constricted to a linear process flow
Aseptic Process Development, Validation, and Evaluation:
- Robots offer extreme repeatability and precision in process
- Programmable recipes and slowed down step-through motions allow for fine-tuning the most minute details of your process and test runs as needed
- Electronic batch records can be exported for highly detailed data and analysis
- Environmental monitoring can be used confirm aseptic environment, along with temperature and pressure management within integrated isolated barrier systems
- Training automated robots to follow a process will always be more reliable than training a team of human operators and trusting them to follow a process
Considerations for multi-product facilities:
- High yield and high potency products
- Minimizing product loss and overall risk to products and operators
- Flexible format machines allows for rapid changeovers, a single machine can process a variety of products in a variety of container formats
- Scalability of operations as drug development moves from research to commercial production
- Programmable recipes allow for simplicity in preparing machine for different products